А вместо сердца - пламенный мотор. Отечественного производства
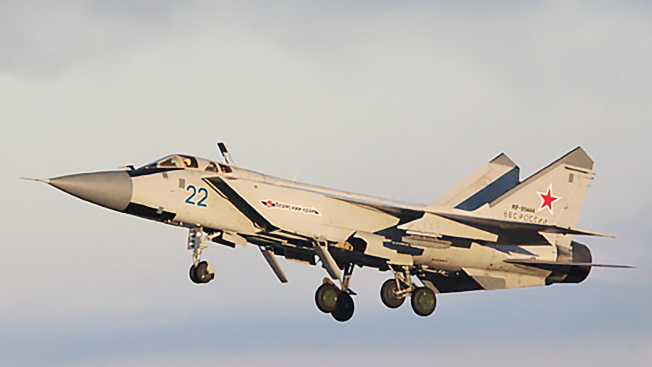
Российское двигателестроение ругали часто, хоронили не раз, а уж слов скепсиса и недоверия успехам было просто не счесть. Естественно, критиковать всегда легче, чем предлагать конструктивные меры по выправлению ситуации, которая сложилась после 1991 года на предприятиях, выпускавших авиадвигатели для нашей гражданской и военной авиации.
У последней черты
Лучше всего эту ситуацию охарактеризовал академик и великий наш конструктор Генрих Васильевич Новожилов, с которым мне посчастливилось пообщаться на тему проблем российского авиапрома.
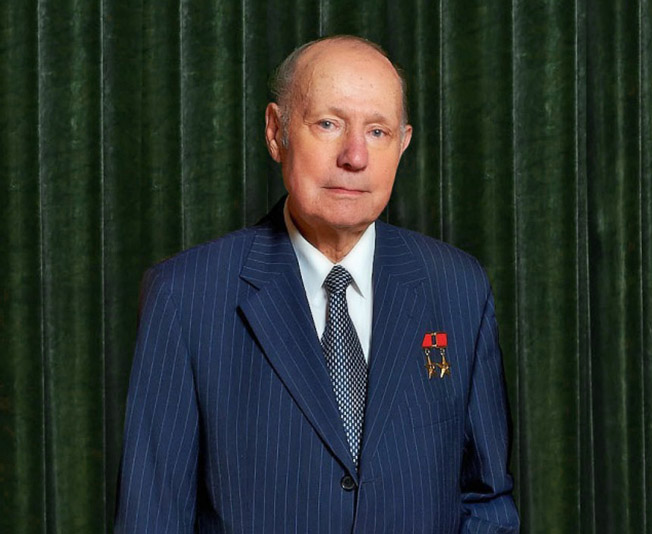
Он рассказал о следующем. В 1990-е годы - в результате изменений правил и повышения требований IKAO - наши авиадвигатели стали «не пригодны для полетов» по причине шумности и неэкологичности. Под действие запрета попали самолеты, сертифицированные по летной годности после 1977 года: Ту-154 всех модификаций, Ту-134, Ил-62, Ил-76, Ил-86, Ил-18, Ан-12, Ан-24 и Ан-124. То есть, практически весь авиапарк, доставшийся России после развала СССР. Единственными самолетами, на которых можно было летать за границу, оказались Ту-204, Ил-114, Ил-96-300 и Ан-124-100, но таких самолетов в эксплуатации у России было не так много.
В качестве быстрых мер авиастроительным компаниям «Ильюшин» и «Туполев» было предложена переделка самолетов под зарубежные двигатели, такие как Rolls-Royse или Pratt & Whitney. С этими фирмами были заключены соответствующие договоры.
К чести наших авиастроителей переделка прошла в рекордные сроки, но вышли проблемы с поставками двигателей. Получился безрадостный парадокс: самолеты, переделанные под зарубежные двигатели, стоят на земле, а отечественные производители двигателей сидят без заказов.
Бедственное положение в двигателестроительной отрасли вылилось в многочисленные протестные акции работников предприятий. Ситуация складывалась критическая: без собственных двигателей сохранение и развитие авиапромышленности было под большим вопросом. Положение усугубляло активное вытеснение из неба России отечественных самолетов полученными по лизингу «Боингами» и «Эйрбасами».
Единственное, что хоть как-то спасало наш авиапром, так это поставки самолетов и вертолетов для военной авиации. Но государственные программы вооружений не бездонны, в отличие от возможностей рынка гражданской авиации - как внутреннего, так и международного. Поэтому не удивительно, что в публикациях СМИ об отечественных авиадвигателях говорилось не о светлом будущем, а о предстоящей неизбежной стагнации и смерти отрасли. Любая положительная информация или появление модернизированных двигателей воспринимались со скепсисом: мол, все это советские, «устаревшие до рождения» изделия.
Такое же отношение вызвала новость об указах президента РФ о создании на базе ФГУП «ММПП «Салют» и «Управляющей компании «Объединенная двигателестроительная корпорация» (ОДК) новой структуры - Научно-производственного центра газотурбостроения. Тогда, в 2007 году, многие эксперты восприняли эти новости, как очередные кадровые и структурные изменения, которые отразятся лишь на контроле финансовых потоков и ускорении процедуры банкротства предприятий. Ведь в 2003 году - после проведения предыдущей административной реформы в двигателестроительной отрасли - показатель роста объема производства снизился до рекордно низкого значения в 1,5 процента.
Смерть отрасли, которую уже пророчили эксперты и аналитики, автоматически ставила крест и на развитии авиационных комплексов военного назначения.
Последняя надежда оставалась на сотрудничество с украинскими предприятиями «Мотор Сич», «Зоря-Машпроект» и «Ивченко Прогресс». Но соседи, которым достались в наследство мощнейшие советские предприятия, раз за разом срывали по срокам контракты на поставку в Россию авиационных комплексов и боевых кораблей...
Тихая промышленная революция
Собаки лают, а караван идет. Именно так и произошло с нашей отраслью двигателестроения. Тихая техническая и финансовая, административная и структурная революция прошла вне зоны внимания записных аналитиков. Правильно было бы назвать эту революцию - цифровой, так как наши двигатели теперь работают под управлением бортовых компьютеров, цифровых блоков и новейшей аппаратуры.
С появлением централизованной управляющей структуры - холдинга «ОДК» - метастазы, терзавшие отрасль, постепенно сошли на нет.
В цеха предприятий стали поступать современное оборудование, станки и измерительная аппаратура. Была налажена внутренняя интеграция между предприятиями холдинга: в сборке любого двигателя участвовало сразу несколько предприятий. Таким образом, была обеспечена полная занятость всех специалистов, и, как следствие, прекратилась текучка кадров. Мало того, на предприятия пришла молодежь, которая с удовольствием (и за достойную зарплату) стала работать на новых станках.
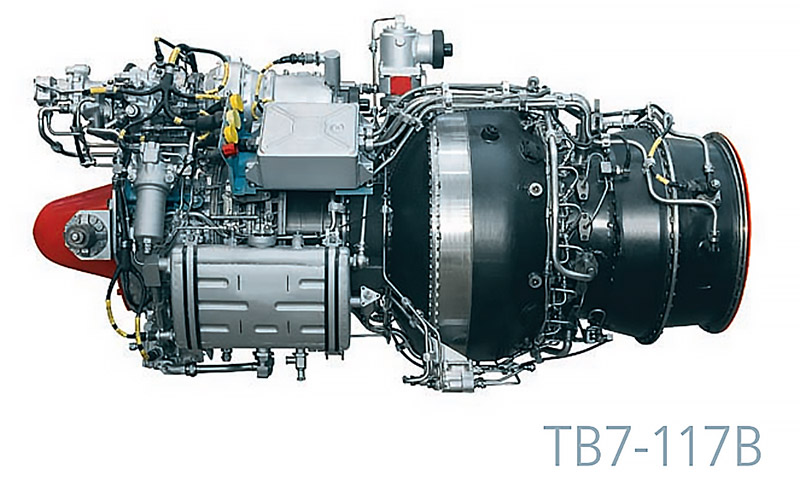
Результаты этой промышленной революции, сказались и на темпах производства. В качестве примера приведу работы по созданию двигателей ТВ7-117, которые проводит «ОДК-Климов», кстати, вновь созданное на основе КБ имени Климова современное предприятие.
Так вот, в 2016 году был запущен испытательный стенд для этого двигателя, а ровно через год начались летные испытания в ГЛИЦ имени М.М. Громова в Жуковском. Такие темпы были немыслимы не только в 1990-е, но и во времена СССР.
Двигатель ТВ7-117 разработан для трех авиакомплексов: военно-транспортного самолета Ил-112, вертолета Ми-38 и самолета Ил-114. Маленький, но очень важный в нынешние «санкционные дни» нюанс: двигатель собирается полностью из российских комплектующих.
Такая же история произошла и на «ОДК-Сатурн». В 2017 году нашему президенту продемонстрировали новый испытательный комплекс для морских газотурбинных двигателей (ГТД) М70ФРУ и М90ФР, а уже в 2018 году М70ФРУ начали поступать на предприятия собирающие корабли для ВМФ России.
«Создавая эти морские газотурбинные двигатели, мы шли по пути унификации, а также закладывали возможность разработки на их базе двигателей следующего поколения, - отмечает генеральный конструктор АО «ОДК» Юрий Шмотин. - Преимуществом российских морских ГТД в сравнении с украинскими, изготовленными по технологиям 60-80-х годов, является повышенная надежность изделий, обусловленная обеспечением жестких требований к изготовлению наиболее ответственных деталей»
Цифровизация коснулась не только систем управления создаваемых двигателей, но и всех технологических процессов на предприятиях двигателестроительной отрасли. Широко внедрены так называемые аддитивные технологии, которые позволяют выпускать узлы и агрегаты высочайшего качества.
Например, благодаря им создаются пустотелые лопатки турбины, которые не теряют своих прочностных и термостойких качеств, но при этом уменьшают массу двигателя. Точность в изготовлении топливных насосов, агрегатов распределения топлива и систем автоматического управления (САУ), которая была освоена на «ОДК-Стар» позволила не только снизить расход топлива, но и избежать вечной «болезни» двигателя - помпажа.
Помимо этого, специалистами «ОДК» были решен вопрос поставок качественных запасных частей, в том числе таких, по которым отсутствует полнота технической документации. Достаточно иметь образец нужного агрегата - с него и снимается «цифровая копия». Потом с помощью специального программного обеспечения производится доведение полученных данных до современных требований к качеству. Именно таким методом на «ОДК-Пермские моторы» было восстановлено производство двигателя Д-30Ф6, которым комплектуется истребитель-перехватчик, а отныне и носитель гиперзвукового оружия - МиГ-31.
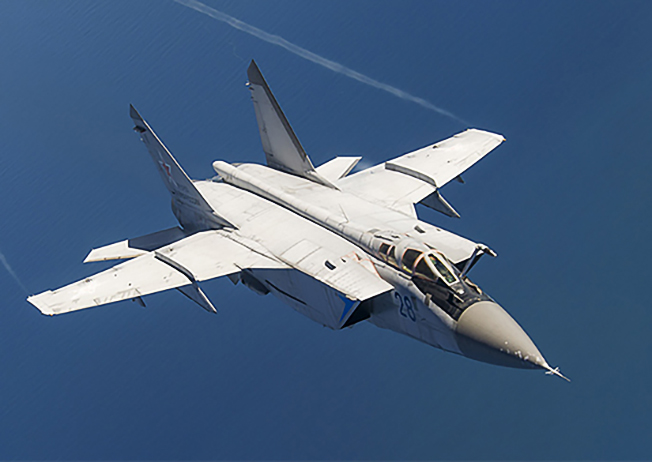
Головная боль авиатехника в воинской части - это диагностика работоспособности двигателя и определение его межремонтного ресурса, который зависит от условий эксплуатации, особенно во время боевых действий. На помощь войсковым эксплуатантам пришли конструкторы и инженеры «ОДК-Климов».
Теперь на всех двигателях ВК-2500 (на них летают вертолеты Ми-28Н, Ка-52 и Ми-171Ш) устанавливают счетчики наработки и контроля (СНК-78). Такой счетчик, работая в паре с электронным блоком автоматического регулирования и контроля (БАРК-78), позволяет точно определить реальное состояние двигателя и правильно рассчитать ремонтный ресурс.
Таким образом, «неожиданность» поломок двигателя в полете исключается полностью. Побочным эффектом от внедрения СНК-78 и БАРК-78 стало продление ресурса эксплуатации двигателя, что естественно приятно порадовало и авиаспециалистов, и финансистов нашего Минобороны.
«Калибры» долетают до цели
Специализация холдинга «ОДК» распространяется и на ракетную отрасль. Речь не только о знаменитых двигателях РД-180, которые доказали свое мировое лидерство и поэтому их покупают США для ракет «Атлас-5». К слову, и успешные запуски ракет «Союз» с нашего космодрома «Восточный» обеспечены двигателями производства «ОДК-Кузнецов» - РД-107 и РД-108.
Но я хочу сказать о других ракетах. Их хорошо знают боевики из «Исламского государства» (запрещенная в РФ организация) - те, кому удалось выжить. Да-да, именно о «Калибрах» хочется сказать, двигатели для которых также делают на предприятиях российского двигателестроительного концерна.

Качественная боевая работа «Калибров» напрямую зависит от надежности работы двигателя ТРДД-50. Нареканий к нему со стороны наших военных не было и нет. Мы свои «Калибры», в отличие от «Томагавков», во время боевых действий не теряли. Все русские ракеты попали точно в цель!
Подводя итоги краткого обзора состояния дел с российскими двигателями можно констатировать факт: наша двигателестроительная отрасль не только возродилась, но и уверенно продолжает развиваться, выпуская качественные и современные двигатели для военной авиации и военного флота.
И да, прогнозы о смерти отечественного двигателестроения не сбылись. Россию и на этом направлении развития остановить не удалось - ни саботажем украинских партнеров, ни санкциями «коллективного Запада».