Директор по развитию ПАО «Звезда» Александр Зиновьев: «Большинство строящихся сегодня российских кораблей - с нашими двигателями или редукторами»
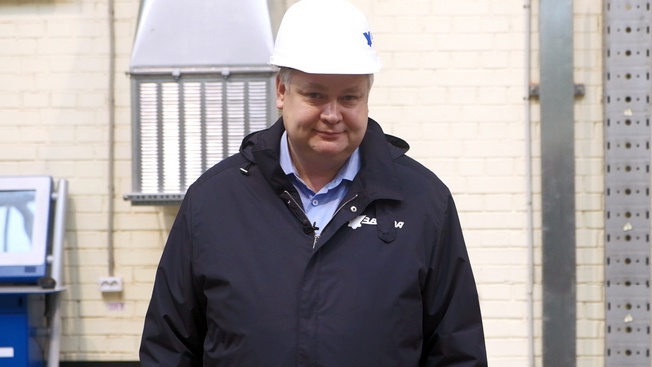
Петербургское ПАО «Звезда» - одно из ведущих предприятий российского дизелестроения, разработчик и производитель высокооборотных двигателей и редукторов для судостроения, железнодорожного транспорта и малой энергетики. Сегодня продукция предприятия применяется во многих проектах строящихся кораблей и катеров российского Военно-Морского Флота. Длительный спад в объёме заказов предприятия, продолжавшийся последние десятилетия вплоть до 2014 года, сменился бурным ростом в связи с программой по строительству новых кораблей для ВМФ России и потребностью в решении глобальных задач в области импортозамещения в судостроении. Это неизбежно привело к необходимости комплексно менять подход к организации производства.
О том, как выполняется гособоронзаказ, какие меры принимаются для увеличения темпов выпуска и в каком направлении планируется дальнейшее развитие дизелестроительного завода еженедельнику «Звезда» рассказал директор по развитию ПАО «Звезда» Александр Зиновьев.
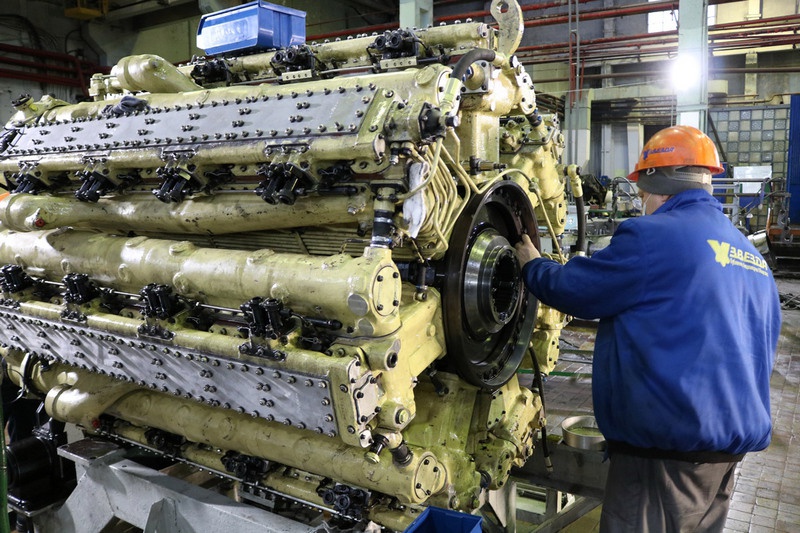
«Мы не используем в производстве продукцию импортного производства»
- Александр Михайлович, на чём сегодня сосредоточены усилия руководства и коллектива ПАО «Звезда»?
- Основная задача - выполнение государственного оборонного заказа. С 2014 года объём таких заказов резко возрос, можно сказать, десятикратно. Возникла объективная необходимость менять подход к организации производства.
Надо понимать, что сам по себе дизельный двигатель - это сложное техническое изделие, состоящее из порядка 10 тысяч комплектующих только по наименованиям. В его изготовлении задействованы десятки станков, несколько сотен специалистов основного производства, выполняются тысячи технологических операций. Одновременно с выпуском двигателей и дизель-генераторов завод все эти годы вёл разработки и освоение в производстве новых модификаций редукторных передач.
Каждое изделие проходит на предприятии полный цикл - от литья заготовок и обработки деталей до сборки готовой продукции и проведения стендовых испытаний. В соответствии с требованиями заказчика мы не используем в производстве продукцию импортного производства. Основная часть деталей и узлов изготавливается непосредственно на «Звезде», остальное - поставки отечественных предприятий.
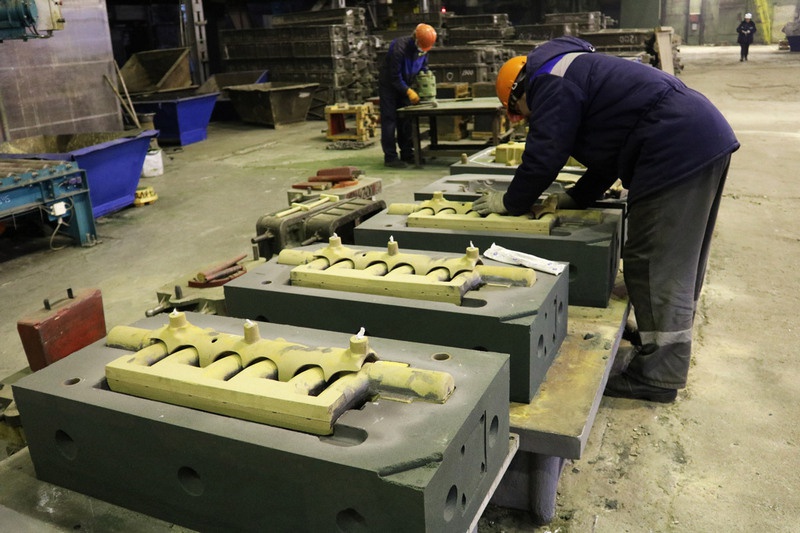
Сегодня помимо новых контрактов на срок до 2023 года нам приходится работать с тем, что накопилось с 2017-2018 годов. В наших жёстких условиях ограниченных ресурсов результат неплохой: за 2018-2020 гг. удалось почти в два раза сократить отставание по заказам, и мы надеемся к началу 2022 года выйти на выполнение программы в срок.
- За счёт чего удалось достигнуть таких результатов?
- За последний год мы практически удвоили выработку. Увеличили количество производственного персонала, оптимизировали загрузку оборудования, отработали технологические процессы, аутсорсинг, организовали оптимальные графики сменности. Ведущую роль в этом играет развитие производственной системы предприятия в соответствии со стандартами бережливого производства, которым предприятие планомерно занимается уже почти два года.
Благодаря уже внедрённым в повседневную практику инструментам (инструменты системы 5S, стандартизированная работа, создание эталонных рабочих мест и потоков) мы уже можем наблюдать первые результаты. Развитие производственной системы направлено на снижение затрат и обеспечение качества и безопасности за счёт исключения в работе предприятия всех видов потерь. Сегодня на заводе реализован базовый комплекс мероприятий, и в этой области мы видим перспективы для дальнейшего совершенствования.
Далее, нам удалось улучшить обеспечение производства материалами и комплектующими, в том числе за счёт развития аутсорсинга на более высоком уровне. Сформирован пул предприятий-поставщиков, которые поставляют заводу продукцию необходимого качества и в срок.
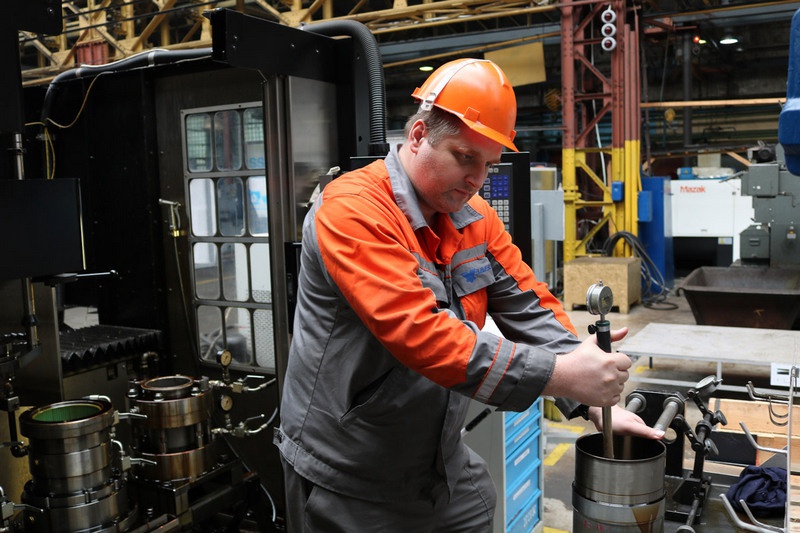
Кроме того, мы приступили к реализации инвестпрограммы, в 2021 году внедрим в работу три крупных обрабатывающих центра, трубогибы, сварочное оборудование, оборудование для мойки деталей и узлов, а также контрольно-измерительную машину. Оптимизация технологий металлообработки - важнейший фактор повышения производительности труда.
«Мы работаем над модернизацией самой востребованной линейки наших двигателей и расширяем номенклатуру изделий»
- Какие задачи ставит перед собой «Звезда» на перспективу? В каком направлении будет развиваться предприятие?
- Безусловно, «Звезда» есть и будет оставаться одним из ведущих российских разработчиков и производителей высокооборотных дизельных двигателей и агрегатов на их базе, в первую очередь, для обеспечения потребностей российского Военно-Морского Флота. Мы работаем над модернизацией самой востребованной линейки наших двигателей размерности ЧН16/17. Эти работы ведутся в рамках ОКР по программе «Развитие ОПК РФ». Основные цели модернизации заключаются в увеличении ресурса двигателей, повышении экономичности, снижении расхода топлива (на 10%) и масла, снижении трудоёмкости обслуживания за счёт исключения механических регулировок. Для этого будет применена современная электронная система топливоподачи. Внедрение локальной системы управления обеспечит автоматизированную диагностику состояния двигателя, его защиту, автоматизированное управление и гибкое регулирование режимов его работы. Кроме того, будет усовершенствован узел включения отсека, конструкция поршней и клапанов с применением новых материалов. Первый модернизированный двигатель семейства выйдет на испытания уже в середине 2021 года.
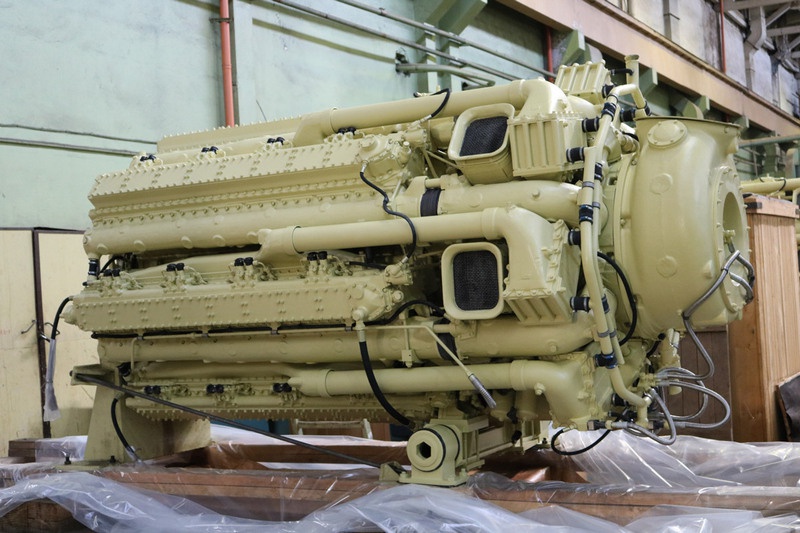
Второе направление связано с редукторными передачами. Напомню, что в 2002 году «Звезда» была определена головным российским разработчиком и производителем редукторов для судовых энергетических установок Министерства обороны РФ. С этого времени предприятие разработало и успешно освоило в производстве ряд изделий передаваемой мощностью до 20.000 кВт для дизель-дизельных, дизель-газотурбинных и газотурбинных силовых установок кораблей различных проектов. В том числе завод участвует в проектах импортозамещения продукции зарубежных производителей на отечественном флоте.
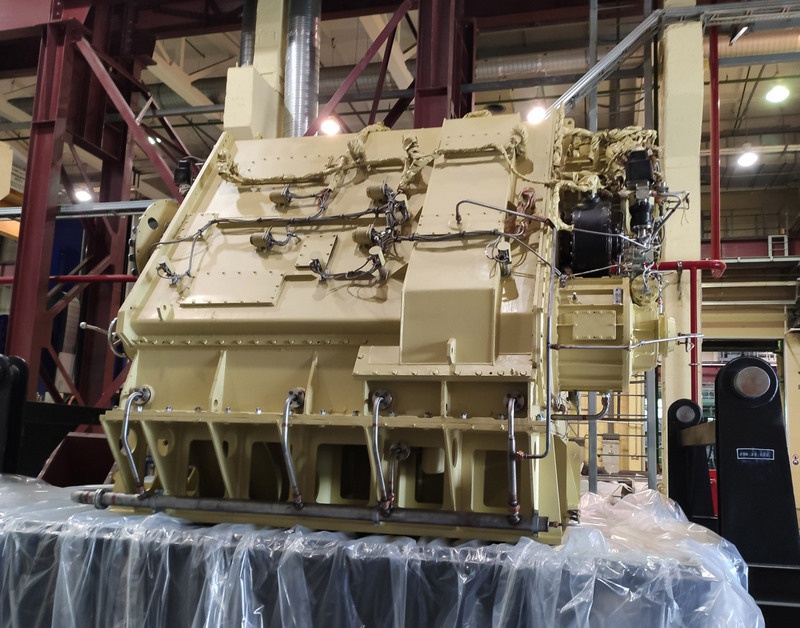
Справка
В апреле 2014 года Президентом Российской Федерации Владимиром Путиным была поставлена задача перед коллективом ПАО «Звезда» по обеспечению редукторными передачами всех типов строящихся, ремонтируемых и перспективных проектов кораблей ВМФ России. За этот период предприятием был разработан и поставлен на серийное производство ряд тяжёлых передач для новейших кораблей ВМФ РФ различных проектов.
По поручению Президента Российской Федерации завод в рамках программы импортозамещения приступил к освоению выпуска новых редукторов для проектов 22350, 12322 и 12061, ранее поставлявшихся с Украины.
Благодаря интенсивному развитию редукторного направления и востребованности этой продукции на российском рынке мы видим плавное смещение фокуса в нашей продуктовой линейке от непосредственно дизельных двигателей в сторону дизель-редукторных агрегатов и продукции редукторного производства (реверс-редукторы, сложные редукторные комплексы, различные виды зубчатых передач и пр.). Эта номенклатура будет расширяться с одновременным увеличением объёма выпуска. Если сегодня редукторные передачи составляют порядка 20% объёма производства, то в планах на ближайшие годы - увеличить их долю до 50%.
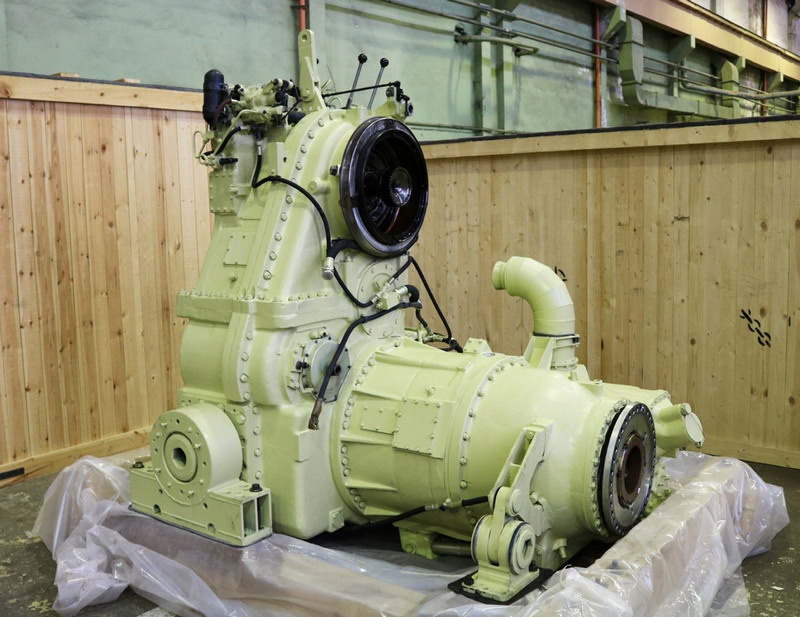
Третье направление касается возобновления системной работы с потребителями по сопровождению жизненного цикла выпущенных дизельных двигателей и редукторов, находящихся в эксплуатации за пределами гарантийных обязательств. Речь идёт об авторском надзоре, обеспечении ЗИП и проведении ремонтов различного уровня сложности, включая капитальные. Доля выпускаемых предприятием комплектующих, предназначенных для обеспечения потребностей эксплуатации, будет увеличена с 5% до 20% объёма поставок. Для этого мы выстраиваем порядок взаимодействия с профильными департаментами Министерства обороны и Объединённой судостроительной корпорацией, в перспективе планируя стать крупным участником рынка ремонта и обслуживания дизельных двигателей и редукторов судового назначения.
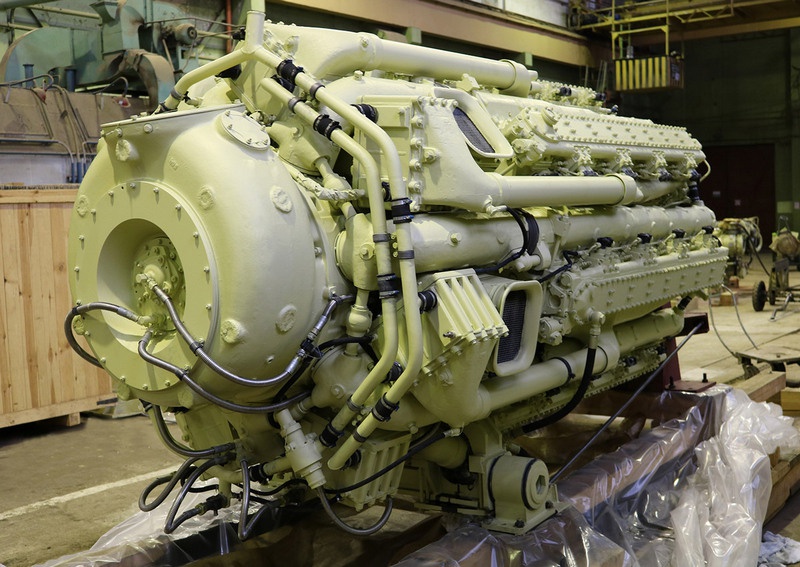
«Раньше в Российской Федерации редукторы такой мощности никогда не выпускались»
- Вы перечислили основные направления, на которых предприятие сосредоточится в ближайшие годы. Какие ещё потенциальные точки роста можно назвать?
- Для развития мы можем опираться на свои ключевые технологические компетенции - литьё и механообработку. Это те области, где наше предприятие обладает значительным опытом, квалифицированным персоналом и развитой технической базой. Поэтому завод планирует развивать кооперацию с крупными российскими машиностроительными предприятиями и изготавливать для них различные комплектующие (отливки, поковки, зубчатые передачи). Такой опыт у нас есть - «Звезда» уже поставляет ряд изделий по заказу производителей железнодорожной техники.
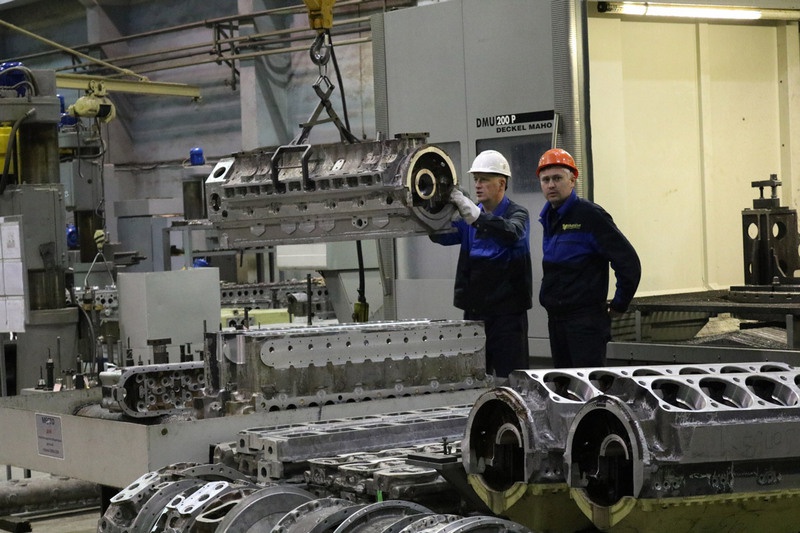
Определённые технологии, которые мы развиваем в интересах основного производства, могут найти применение и в других проектах. Благодаря освоению технологии изготовления крупногабаритных алюминиевых корпусов для редукторов мы получили современный участок резки и сварки листового металла и профилей. Это даёт возможность выстраивать производственное партнёрство с другими компаниями, например, изготавливать алюминиевые рамы для одного из игроков рынка автономной генерации. Впрочем, сотрудничество с производителями коммерческого оборудования не помешает собственным планам по увеличению объёма выпуска дизель-генераторов для Министерства обороны.
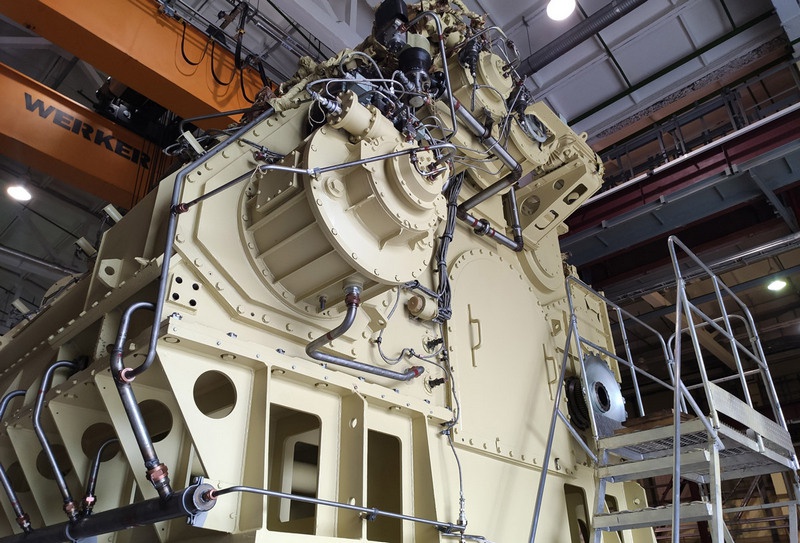
Справка
Редукторы Р055 ПАО «Звезда» для первой отечественной силовой установки фрегата пр.22350 успешно прошли квалификационные испытания, а также испытания в составе дизель-газотурбинного агрегата, разработчиком и изготовителем которого является НПО «Сатурн». Решением квалификационной комиссии предприятие признано готовым к серийному выпуску и поставке изделий.
Редуктор Р055 обеспечивает полную мощность переднего хода при работе газотурбинного двигателя 27.200 л.с., при работе дизельного двигателя - 5.069 л.с.; его вес составляет около 40 тонн. Это сложное техническое изделие, состоящее из порядка 5.000 номенклатурных единиц комплектующих. При производстве используются только комплектующие собственного и российского производства, для чего потребовалось создать широкую сеть межзаводской кооперации.
Раньше в Российской Федерации никогда не выпускались редукторы такой мощности.
- Что Вы считаете основным достижением завода в 2020 году?
- Самое главное событие года - завершение квалификационных испытаний редукторов для первой отечественной силовой установки фрегата пр.22350. Они также прошли испытания в составе дизель-газотурбинного агрегата, разработчиком и изготовителем которого является НПО «Сатурн».
Раньше в Российской Федерации передачи такой мощности никогда не выпускались. Редуктор обеспечивает полную мощность переднего хода при работе газотурбинного двигателя 27.200 л.с., при работе дизельного двигателя - 5.069 л.с.; его вес составляет около 40 тонн. Это сложное техническое изделие, состоящее из порядка 5.000 номенклатурных единиц комплектующих.
Данная конструкция - результат нескольких лет работы коллектива. Освоение производства этих редукторов длилось с 2017 года в рамках программы импортозамещения продукции украинского производства. Специалисты завода провели доработку технической документации и выполнили большой объём работ по подготовке производства, изготовлению деталей и сборочных единиц, проведению сборки и испытаний, включая создание уникального испытательного стенда.
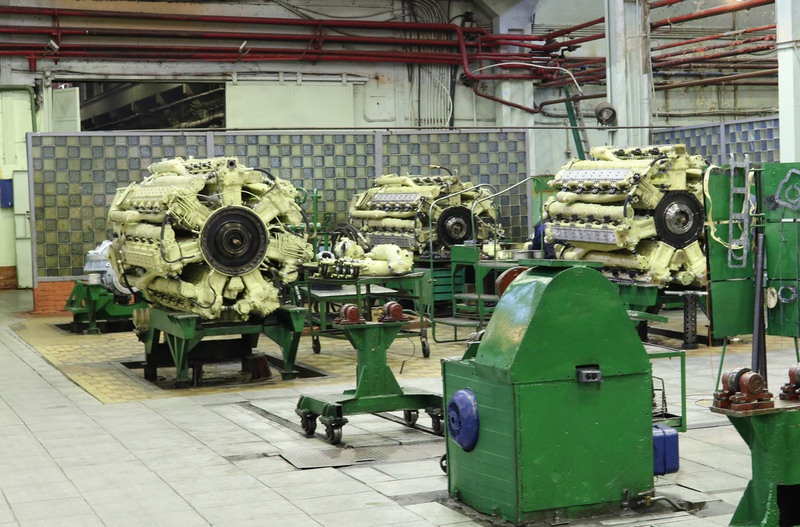
При производстве используются только детали и узлы собственного и российского производства, для чего потребовалось создать широкую сеть межзаводской кооперации в отсутствие развитого рынка компаний необходимого профиля. Работы велись в условиях загруженности собственного технологического оборудования значительным объёмом заказов и неизбежного появления «узких» производственных участков.
Несмотря на это, все трудности были успешно преодолены, и теперь «Звезда» может выпускать такие передачи серийно, полностью обеспечивая потребности российского флота.
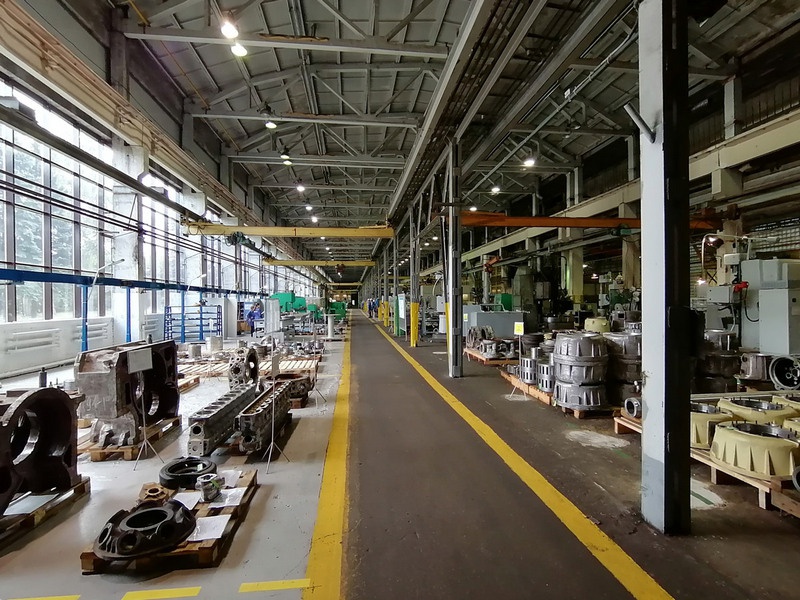
Менее масштабно, но столь же важно для завода - в 2020 году мы наладили устойчивый выпуск двигателей и дизель-генераторов в маломагнитном исполнении. Эти изделия изготавливаются из материалов, обладающих особыми свойствами, востребованными в определённых областях судостроения. Наши специалисты освоили навыки обработки таких материалов в соответствии с требованиями заказчика по уровню магнитной проницаемости и вышли на требуемый по графику темп производства комплектов оборудования.